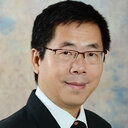
Wei ZhouNanyang Technological University | ntu · School of Mechanical and Aerospace Engineering
Wei Zhou
BEng (Tsinghua, 1985); PhD (Cambridge, 1991)
About
319
Publications
75,708
Reads
How we measure 'reads'
A 'read' is counted each time someone views a publication summary (such as the title, abstract, and list of authors), clicks on a figure, or views or downloads the full-text. Learn more
7,741
Citations
Introduction
Additive manufacturing, including selective laser melting, laser direct energy deposition, and cold spray coating.
Additional affiliations
December 2013 - June 2014
April 1992 - present
Publications
Publications (319)
Post-heat treatments are vital to produce superior nickel-based superalloys with high performance by directed energy deposition (DED) for harsh service conditions. In this work, directed energy deposited Inconel 718 samples underwent varied heat treatment routes including the direct aging heat treatment (DA), standard solution treatment plus aging...
Among the various fusion-based additive manufacturing processes, wire arc additive manufacturing (WAAM) has the highest deposition rate, which is beneficial for fabricating large volume components. The WAAM process usually begins with printing on a substrate, that could act as a functional part of the component. To study the possibilities of fabric...
Micro-vibration measurement is crucial for fault diagnosis of robot joints. An increasing number of fiber Bragg grating (FBG) vibration sensors have been developed based on different sensing principles. However, these FBG vibration sensors cannot be applied to high-frequency vibration measurement or embedded into robot joints due to their low reson...
Oxidation is a common issue in directed energy deposition (DED) based additive manufacturing (AM) processes. Severe oxidation is usually considered to be detrimental, which should be avoided. However, it is found that the surface oxidation of the deposited materials can also lower the laser reflectance, thereby increasing the utilization rate of la...
Additive manufacturing (AM) is a transformative approach to fabricating metal components in the industry. However, it is challenging for fusion-based AM to fabricate metallic materials, particularly austenitic stainless steels, which have fine equiaxed grains without the formation of undesirable intermetallic phases due to its intrinsic high therma...
In this paper, laser aided additive manufacturing (LAAM) of stainless steel 316L (SS 316L) in a controlled argon environment was investigated. The controlled argon environment can significantly reduce the oxidation and fundamentally change the process conditions. It was found that after inhibiting oxidation, the surface of the deposited 316L showed...
运用自主研发的爬壁机器人研究焊接速度和焊接电流对竖向高速熔化极气体保护焊(gas metal arc welding,GMAW) 驼峰焊缝的影响. 结果表明,焊接速度或焊接电流超过某一临界值时,竖向高速GMAW 会形成驼峰焊缝,且熔池中由电弧压力、熔滴冲击力和重力作用下产生的动量很大的后向液体流是竖向高速GMAW 形成驼峰焊缝的主要原因. 同时,焊接速度和焊接电流显著影响驼峰焊缝形貌. 当焊接电流不变时,随焊接速度提高,驼峰焊缝的驼峰间距和驼峰高度先稳定减小,后缓慢减小,而焊缝宽度则稳定减小;当焊接速度不变时,随焊接电流增加,驼峰焊缝的驼峰间距先增加后减小,驼峰高度则是先增加后不变,而焊缝宽度则稳定增加. 此外,焊接速度过小或焊接电流过大均会造成金属液下淌。
Laser powder bed fusion (LPBF) is a fusion-based additive manufacturing process. It has the advantage of allowing the manufacturing of metal matrix composites. This advantage arises from its small melting zone and rapid cooling rate, which minimize the risk of reinforcement segregation. In this work, 0.3 wt% and 1.0 wt% Y2O3 nanoparticles were adde...
The additive noise in the condition monitoring system using fiber Bragg grating (FBG) sensors, including white Gaussian noise and multifrequency interference, has a significantly negative influence on the fault diagnosis of rotating machinery. Spectral subtraction (SS) is an effective method for handling white Gaussian noise. However, the SS method...
In this study, Al–70Si alloy was prepared by laser cladding. The effect of microstructure on the mechanical and thermo-physical properties was elucidated by comparing specimens prepared by laser cladding and casting methods. It is found that the laser cladding process can effectively reduce the formation of coarse primary silicon, which inevitably...
Metal-matrix composite (MMC) coatings are advanced materials that can be customised to meet industrial requirements such as high strength-to-weight ratio and wear-resistance. Cold spray (CS) technology can be used to develop these MMC coatings. It is a low temperature deposition method, which does not involve particle melting and thus preserves the...
Laser directed energy deposition (L-DED) is one of the main multi-layer joining technologies for additive manufacturing (AM). It has shown great potential and has been increasingly used in the past two decades. As this process is usually operated without chamber, oxidation becomes one of the main issues that influence the bonding strength of the DE...
Decarburization is an unwanted carbon-loss phenomenon on the surfaces of a material when they are exposed to oxidizing environments at elevated temperatures. Decarburization of steels after heat treatment has been widely studied and reported. However, up to now, there has not been any systematic study on the decarburization of additively manufactur...
Decarburization deteriorates the surface mechanical properties of steel. It refers to the loss of carbon from steel’s surface when exposed to an open-air environment in elevated-temperature conditions. Despite the short interaction time and fast thermal cycle of the laser surface-hardening process, decarburization may still occur. This paper invest...
A metal matrix composite with Inconel 718 as the base metal and yttrium oxide (Y2O3) as the reinforcement particles was fabricated by the laser powder bed fusion technology. This paper presents a comprehensive study on the influence of the Y2O3 reinforcement particles on the microstructures and mechanical properties of the heat-treated printed comp...
As one of the key technologies of Industry 4.0, additive manufacturing (AM) has been gaining rapid momentum in R&D and industry applications. However, achieving high consistency of material properties and dimensional accuracy of the additively manufactured parts remains a challenge. Hence, it is necessary to make the AM process intelligent to addre...
A two‐step process, including the pre‐metallization of the SiC ceramic by Ag‐26.7Cu‐4Ti+B4C and the followed brazing with the Al based filler alloy, was developed to join 2219 aluminum alloy and the metallized SiC. The influence of metallization temperature and the B4C addition on the microstructure and mechanical properties of the joint was analyz...
Additive manufacturing has been regarded as a revolutionary technology and gained fast development in the past two decades. However, it is largely a trial-and-error process to find the optimal printing strategy, and the poor reproductivity poses a problem for quality control. It would help to tackle the problems by making the additive manufacturing...
Laser shock peening is a surface enhancement method that is capable of altering the mechanical properties of materials. High energy pulsed laser beam is used to create shock waves that propagate through the material to induce compressive residual stresses. These compressive stresses are often beneficial for engineering components as they increase t...
Drilling, one of the most used machining processes, has wide application in different industrial fields. Monitoring the system health and operation status of the drilling process is essential for maintaining production efficiency. In this study, a convolutional neural network (CNN), a deep-learning method, is applied to the defect diagnosis of dril...
Repair is a process of restoring the functionality of a damaged component to its original functional state to extend the lifespan of the component. For high-value engineering components, it is often more cost-effective to repair the damaged parts than replace them with new ones. This paper focuses on the utilization of laser directed energy deposit...
316L stainless steel is commonly used for engineering applications owing to its distinguished oxidation and corrosion resistance. However, its yield strength is low at 170–300 MPa, which limits its applications. Adding reinforcements to 316L is a potential method to enhance its yield strength. Laser powder bed fusion (LPBF) process has the advantag...
Additive manufacturing has gained significant attention in recent years. However, oxidation is hard to be avoided especially for the directed energy deposition (DED) processes, which are normally operated in an open environment with inert gas shielding. Excessive oxidation will negatively affect the mechanical properties of the deposited materials....
Laser powder deposition of Inconel 718 superalloy has been considered as a promising technique for the restoration of damaged aerospace components. A novel gradient laser power (GLP) deposition method is proposed to build Inconel 718 thin-wall structures by gradually reducing laser powers. The method not only alleviates micro-segregation but also t...
p>Cold spray is an emerging additive manufacturing process allowing particles to be coated onto surface of base material without melting. In this study, Diamalloy 1005 was successfully coated onto GJL-250 cast iron using a cold spray process, and extensive experiments were carried out to observe the effects of diffusion after heat treatment at 400,...
In article 2100664, Zhou, Nai, and co‐workers show that 304L and 316L have similar compositions. However, a selective laser melted 304L and 316L show a significant difference in grain size and morphology. Their microstructures and mechanical properties are compared using a scanning electron microscope, electron backscattered diffraction, nanohardne...
The current research represents the first systematic study on high temperature oxidation and oxychlorination behaviors of cold sprayed Inconel 718. Tests were carried out at 700 ℃ and cold sprayed Inconel 718 was shown to possess excellent oxidation resistance comparable to that of the bulk Inconel 718. In the oxychlorination condition, a single-la...
The vacuum brazing of dissimilar Al 7075 and Al–25 Si alloy was investigated. The brazing filler was copper foil with a thickness of 20 μm, and the brazing temperature was 560 °C held for 10 min. The average shear strength of the brazed joint of dissimilar Al 7075 and Al–25 Si alloy was 26.4 MPa. The copper layer was found to be dissolved completel...
Cold spray is an emerging additive manufacturing process that allows particles to be coated onto the surface of a base material without melting. It is suitable to repair components made from temperature-sensitive materials, such as grey cast iron, which cannot be easily restored using conventional methods like welding or thermal spray. In this stud...
Joining metals and ceramics plays a crucial role in many engineering applications. The current research aims to develop a simple and convenient approach for dissimilar material joining between SiC and Al alloys. In this work, Al alloys with Si contents varying from 7 wt.% to 50 wt.% were bonded with SiC at a high temperature of 1100 °C by a pressur...
Additive manufacturing (AM) is a transformative approach to fabricating metal components in the industry. However, it is challenging for fusion-based AM to fabricate metallic materials, particularly austenitic stainless steels, which have fine equiaxed grains without the formation of undesirable intermetallic phases due to its intrinsic high therma...
There has been limited research on Ni-based oxide dispersion strengthened (ODS) alloys. To alleviate the drawbacks of the traditional ODS alloy manufacturing method, selective laser melting technology was chosen in this study to successfully manufacture ODS Inconel 718-Y2O3 alloys. Y2O3 nanoparticles were mixed with Inconel 718 powder at different...
Cold spray is a solid-state additive manufacturing process that has been increasingly used for restoration of damaged parts. Due to the nature of powder solid-state bonding, cold spray coatings usually possess pores in the microstructures. Heat treatment has been widely used as a post-processing method to reduce the porosity of cold sprayed coating...
Among various types of stainless steels, 304L and 316L have the most engineering applications. In this work, 304L and 316L powders with similar size distributions and morphologies are used as raw materials for selective laser melting (SLM) using the same parameters. It is found that SLM 304L has two phases, γ‐austenite (∽95%) and δ‐ferrite (∽5%) ph...
Wire arc additive manufacturing (WAAM) is suitable to fabricate large components because of its high deposition rate. In this study, a metal-cored low-alloy high-strength welding filler metal was used as feedstock. Single wall structures were prepared using the WAAM process with different interpass temperatures (150 °C, 350 °C, and 600 °C). No obvi...
In this work, strengthening of 316L stainless steel was achieved through addition of 1 and 3 wt% TiC nanoparticles. The TiC nanoparticles and 316L powders were mixed using low energy ball milling and then processed by selective laser melting. The grains are significantly refined from 16.8 μm to 6.9 μm with the addition of 3 wt% TiC nanoparticles. A...
Fe50Mn30Co10Cr10 high-entropy alloys were prepared by laser cladding technology. The microstructure and phase structure of the cladding layer were analyzed. The effects of laser cladding parameters on mechanical property of the cladding layer were studied. The results show that, the Fe50Mn30Co10Cr10 high entropy alloy cladding layer is composed of...
Cold spray technology using micron-sized particles to produce coatings is increasingly used for reparative tasks in various industries. In a cold spray setup, the gun is usually connected to a robotic arm to deposit coatings on components with complex geometries. For these components, the standoff distance used in the cold spray process has to be l...
Computational Fluid Dynamics (CFD) simulation is an effective method to optimize cold spray process parameters and coating quality. The objective of this work is to construct a CFD model to directly investigate influence of the process parameters such as pressure and carrier gas composition on the particles. This work describes a detailed study of...
Cold spray is an additive manufacturing process increasingly used for repair and restoration of damaged components. A common problem with the technology is the high level of porosity in the as-sprayed coatings. Effort has been made in the past to reduce the porosity level by post-processing methods such as heat treatment in vacuum furnace. However,...
Cold spray is an emerging additive manufacturing technology that is promising to be used for surface repair and enhancement. In this study, Inconel 713 coating was successfully deposited on Inconel 718 substrate using a high-pressure cold spray process. The microstructure and hardness of the coating were studied. The cold sprayed Inconel 713 coatin...
Cold spray is an emerging additive manufacturing process allowing particles to be coated onto surface of base material without melting. In this study, Diamalloy 1005 was successfully coated onto GJL-250 cast iron using a cold spray process, and extensive experiments were carried out to observe the effects of diffusion after heat treatment at 400, 7...
Cold spray is a solid-state powder deposition technique suitable for repair of parts. Use of nominally the same powders from different manufacturers is known to lead to very different porosity levels in the cold spray coatings, so it is important to find an effective method for the powder evaluation. A comparative study was carried out of Ti6Al4V p...
316L stainless steel has a wide range of engineering applications. However, its relatively low yield strength limits its applications. In this work, strengthened 316L stainless steel was fabricated via selective laser melting (SLM) with the addition of 3 wt% micronsized TiC particles. The grains of 316L are significantly refined to approximately 3...
Cold spray is an emerging additive manufacturing technology that is promising to be used for surface repair and enhancement. In this study, Inconel 713 coating was successfully deposited on Inconel 718 substrate using a high-pressure cold spray process. The microstructure and hardness of the coating were studied. The cold sprayed Inconel 713 coatin...
Inconel 713C is a nickel-based superalloy usually considered as a material of poor weldability due to its susceptibility to hot cracking in the heat-affected zones. Cold spray, a solid-state deposition technology that does not involve melting, can be proposed as a methodology to deposit Inconel 713C for surface enhancement of other target component...
Laser surface hardening is an attractive heat treatment solution used to selectively enhance the surface properties of components by phase transformation. A quantitative parameter to measure the efficacy of hardening processes is still lacking, which hinders its application in industries. In this paper, we propose a simple approach to assess the ef...
Varying degrees of strain was imposed to AZ31 hot-extrusion bars by ambient extrusion. Mechanical properties were tested along different loading direction to reveal the effect of working hardening on deformation mechanisms and strain hardening behavior. The results showed that, with the increase of extrusion strain, yield strength increased gradual...
In this study, micron-TiC particles were added into an Inconel 718 matrix to fabricate a metal matrix composite by selective laser melting. The interactions between the micron-TiC particles and the precipitates in the matrix were studied through solutionization treatment. Four holding temperatures 975, 1075, 1175, and 1275 oC were chosen while the...
Conventionally, the main goal of process optimization in selective laser melting (SLM) is to achieve the highest relative density. However, for Inconel 718 (IN718), this study has demonstrated that the highest relative density does not correspond to the best mechanical properties. Moreover, similar relative densities can result in significant diffe...
In this study, Inconel 625 coatings were successfully deposited on 6061 aluminum alloy using a high-pressure cold spray process. The microstructure, mechanical and tribological properties of the coatings were systematically studied. The cold sprayed Inconel 625 coatings had a low porosity level due to the severe plastic deformation of the splats. E...
Considerable research has been carried out to study the laser welding of magnesium alloys. However, the studies are mainly devoted to butt welding, and there has been limited information in the published literature concerning the bead-on-plate laser welding of AZ91D, even though bead-on-plate welding is required for the repair of cast AZ91D parts w...
Vacuum furnace has been used for brazing repair of aerospace components, but it is a slow process which typically takes a few hours. The prolonged heating and cooling cycles could cause some adverse effects on the components such as excessive grain growth. A rapid brazing technique using induction coil was studied to evaluate its suitability for lo...
In this study, we have fabricated a TiC particle strengthened 316L stainless steel metal matrix composite using selective laser melting and characterized the microstructure with a particular focus on the TiC carbides in terms of their crystallography and orientation relationship with the austenitic matrix. Two families of TiC carbides are found to...
Cold spray is an emerging additive manufacturing technology used in the aerospace industry to repair damaged components made of expensive metal alloys. The cold sprayed layer is prone to surface integrity issues such as high porosity and inadequate bonding at the substrate-coating interface, which may cause premature failure of the repaired compone...
To systematically investigate the texture induced anisotropy for magnesium, the microstructure, texture and mechanical properties were tested on samples cut along different orientations from an AZ31 extrusion bar. It shows that microstructure, texture and mechanical properties varied with the angle β between the sample direction and transverse dire...
The local microstructural heterogeneities in a single layer of laser clad hypereutectic Al-50Si alloy over Al7075 substrate has been studied over different applied laser powers. The general microstructure of the laser clad layer, irrespective of the applied laser power, could be described by three distinctive regions from the deposited bead/substra...
The magnet-assisted laser hole-cutting in magnesium alloys was explored systematically with and without using water immersion, including femtosecond laser multilayer center-oriented hole-cutting and millisecond laser helical hole-cutting of both blind holes and through holes. The effect of the magnetic field and water immersion on laser hole-cuttin...
γ-TiAl-based alloys have been studied for decades due to their attractive properties. However, the applications are limited because of their poor formability. Electron beam melting (EBM) is advanced in fabricating components with high complexity. Studies have shown that γ-TiAl alloys can be successfully fabricated using EBM. To further explore the...
With the development of Industry 4.0, additive manufacturing will be widely used to produce customized components. However, it is rather time-consuming and expensive to produce components with sound structure and good mechanical properties using additive manufacturing by a trial-and-error approach. To obtain optimal process conditions, numerous exp...
The effect of ER5356 and ER5087 welding wires on fatigue property of MIG-welded 7N01-T4 aluminium alloy joints was investigated. The microstructure of ER5087 welded joint is similar to that of ER5356 joint. However, the fusion zone of the welding joint with ER5087 has a smaller grain size than that of the joint with ER5356. The fatigue strength of...
A novel femtosecond laser layered ring trepanning (LLRT) technology assisted by external transverse magnetic fields is reported for improving laser trepanning efficiency and quality while reducing hole defects. The influence of key operating parameters on blind-hole geometry trepanned by altering magnetic flux density was discussed. The element com...
Constrained groove pressing (CGP), as a novel severe plastic deformation method, is applied to a two‐phase Mg‐Li alloy at room temperature, 373 K, 423 K and 473 K. The microstructural evolution and mechanical properties of Mg‐Li alloy sheets during CGP are investigated. The optimum mechanical properties are achieved at 373 K after two passes. The t...
316L austenitic stainless steel has a wide range of industrial applications. However, one of the major drawbacks is its low yield strength (170-300 MPa in annealed state). We report a method to strengthen 316L by adding 1 wt% and 3 wt% micron-sized TiC particles using low energy ball milling for the powder feedstock preparation followed by selectiv...
Tungsten/steel joints are desired for fusion reactors and militarily applications, as it could combine the unique properties of these two dissimilar metals. In view of the large differences of physical and chemical properties between W and steel, diffusion bonding is considered to be the proper technique for joining of W to steel. In this paper, di...
Diffusion bonding is an effective method for joining dissimilar materials. In this study, dissimilar metals of MA956 steel and tungsten (W) were diffusion bonded with Ni/Nb composite interlayer. The experiments were carried out at 1050∘C, 20 MPa for 20 min in vacuum by spark plasma sintering (SPS) technique. The microstructure and mechanical proper...
Two different sized SiC particles (~ 60 nm and ~ 1 μm) were mixed into AZ31 alloy by multi-pass friction stir processing (FSP). The microstructure and mechanical properties of the processed material were investigated by optical microscope, scanning electron microscope, and uniaxial tensile tests. After FSP without SiC addition, the grains were refi...
Laser hardening is usually performed in air. Use of a controlled gas atmosphere might produce a direct reaction of the gas with surface and thus provide an opportunity to engineer the surface microstructures. However, few studies are reported on direct gas-assisted laser hardening process. In this paper, a direct gas-assisted laser hardening is dem...
Brazing experiments between tungsten and MA956 ODS steel were conducted at 41050∘C with different holding time to investigate the interface microstructure evolution and mechanical properties of the brazed joints. The interface microstructures were analyzed by the scanning electron microscopy (SEM), energy dispersive spectroscopy (EDS) and X-ray dif...
Pre-compression was conducted on AZ31 magnesium alloy bars to prepare different volume fraction of {101¯2} twins. The effect of twins and related crystal orientation on the corrosion properties of the AZ31 magnesium alloy was studied. With the increase of compression strain which induce more twins, corrosion resistance showed different tendency dur...
Nanoparticles reinforced steels have many advantaged mechanical properties. Additive manufacturing offers a new method for fabricating nanoparticles reinforced high performance metal components. In this work, we report the application of low energy ball milling in mixing nanoparticles and micron 316 L powder. With this method, 0.3 and 1.0 wt% Y2O3...
The numerical simulation on laser trepanning of square-slotted hole and hole array in stainless steel sheets with and without ultrasonic assistance was reported for analyzing the stress fields on the workpieces trepanned. Based on reasonable modification and verification for the established models using corresponding experimental results, the trans...
A novel helical laser hole-cutting (HLHC) technology based on coupled assistance of water-based ultrasonic vibrations and external longitudinal/transverse magnetic fields is reported for cutting holes in nickel super-alloy GH4049 sheets. Effects of external unidirectional transverse and longitudinal magnetic fields on HLHC performance were correspo...
Influence of axial magnetic field on micromachining of silicon crystals by ultraviolet nanosecond laser pulses is orders-of-magnitude stronger than by near-infrared femtosecond pulses. It suggests substantial improvement of silicon micromachining by ultraviolet nanosecond laser pulses.
A systematic investigation was reported for observing and analyzing the process and performance of millisecond laser drilling with and without magnetic assistance and/or assist gas using a self-developed real-time monitoring system based on high-speed photography. The systematic and corresponding comparisons between the effects of longitudinal magn...
Water can act as an effective cooling agent during processing of materials. This can be beneficial especially for surface hardening of steels whereby a rapid quenching rate is desired to generate a hard martensitic surface layer. In this study, the underwater laser hardening of bearing steels is experimentally investigated using a fiber laser. The...
In this work, the effect of multipass friction stir processing (FSP) on the microstructure and impact toughness of an as-cast Al–20Si alloy was investigated. FSP resulted in the breakage of coarse primary Si particles and acicular eutectic Si particles, elimination of porosity, and better homogeneity of Si particles. The average size and aspect rat...
Surface laser treatments are often used on metals and metal alloys to improve the material's hardness and corrosion resistance. Investigating the reasons for this property enhancement is not trivial because the resulting microstructure changes gradually from the surface to the bulk. Here we report a simple serial-sectioning technique to assess the...
Diffusion bonding is an effective technique for joining dissimilar metals. In this paper, tungsten and MA956 steel were diffusion-bonded by Spark Plasma Sintering (SPS) technique with titanium (Ti) foil as an interlayer. The bonded joints were evaluated by metallographic analysis and mechanical tests, and the results reveal that all W/Ti/MA956 join...
Friction stir processing (FSP) and surface mechanical attrition treatment (SMAT) were performed on an AZ31 magnesium alloy to improve the mechanical properties. The microstructure, macro-texture, as well as mechanical properties were investigated by optical microscopy, transmission electron microscopy, X-ray diffractometer and uniaxial tensile test...
A steady magnetic field perpendicular to a laser beam is widely used to improve the rate and quality of laser ablation. Recently, we reported a 69-fold enhancement of laser ablation of silicon using a magnetic field parallel to a laser beam. To understand the fundamental mechanisms of that phenomenon, multipulse magnetic-field-enhanced ablation of...
Underwater laser hardening might produce better surface mechanical properties than conventional laser hardening in air due to additional cooling effect by water. However, it has not been studied in detail. This study investigates the effect of water layer on laser surface hardening of AISI 1055 steel. It is found that laser surface hardening is fea...
Laser surface hardening, used to achieve hardened surface without affecting bulk properties of steels, generally employs continuous-wave laser to do the job. The purpose of this paper is to systematically investigate the use of different pulsed lasers for surface hardening of 50CrMo4 steel. A continuous-wave laser and various pulsed lasers with pul...